Preventive
Maintenance
Regular maintenance can improve efficiency, extend the system's lifespan, and prevent costly breakdowns.
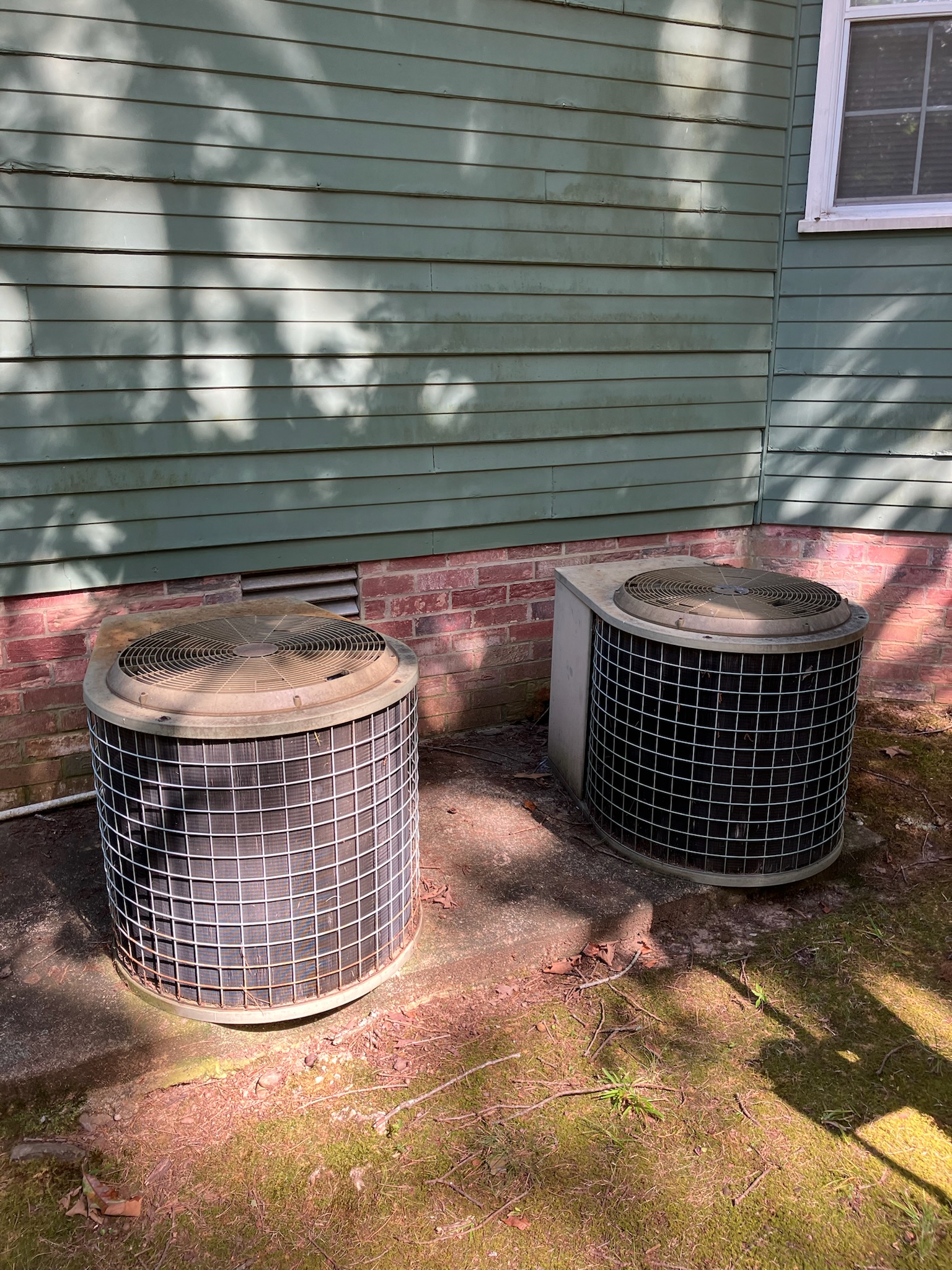
- Regular Inspections. Conducting routine inspections is fundamental to preventative maintenance. This involves a thorough examination of equipment to identify any signs of wear, damage, or potential issues. Inspections allow maintenance personnel to detect problems early on, preventing them from developing into more significant issues that could lead to equipment failure.
- Cleaning of Coils and Filters. Coils and filters play a crucial role in the efficiency of various systems, such as HVAC units. Regular cleaning is essential to prevent the accumulation of dust, dirt, or debris, which can hinder performance and lead to overheating. Clean coils and filters ensure optimal airflow and energy efficiency, reducing the workload on the equipment.
- Lubrication of Moving Parts. Moving parts within machinery can experience friction and wear over time. Lubrication is a key preventative maintenance task that involves applying the appropriate lubricants to these components. This minimizes friction, reduces heat generation, and prevents premature wear, contributing to smoother operation and a longer lifespan for the equipment.
- Checking for Leaks. Fluid leaks can be detrimental to the performance of machinery and can lead to safety hazards. Preventative maintenance involves a regular check for leaks in hydraulic, pneumatic, or other fluid systems. Identifying and repairing leaks promptly helps maintain the integrity of the system and prevents potential environmental contamination.
- Calibration of Equipment. Many types of equipment rely on precise measurements and settings. Regular calibration ensures that instruments and controls are accurate and reliable. This is particularly crucial in industries where precision is vital, such as manufacturing or healthcare. Properly calibrated equipment contributes to consistent output quality.
- Tightening of Loose Connections. Vibrations and normal wear and tear can loosen connections in equipment over time. Preventative maintenance includes checking for loose bolts, nuts, electrical connections, or other fasteners. Tightening these connections prevents issues such as electrical malfunctions, mechanical failures, or even safety hazards.
- Replacement of Worn Parts. As components wear out over time, they may need to be replaced before they fail. Preventative maintenance involves monitoring the condition of parts and replacing them as needed. This proactive approach prevents unexpected breakdowns and ensures that the equipment continues to operate reliably.
- Monitoring and Recording Data. Keeping detailed records of equipment performance, maintenance activities, and any abnormalities observed during inspections is essential. Monitoring data over time allows maintenance teams to identify patterns, predict potential issues, and optimize maintenance schedules for greater efficiency.
- Utilizing Technology. Modern technology, such as predictive maintenance tools and sensors, plays a significant role in enhancing preventative maintenance efforts. Utilizing data analytics and monitoring systems can help predict when equipment is likely to fail, allowing for more strategic and efficient maintenance interventions.
Reach out to us today.
Preventative maintenance is a multifaceted approach that involves regular inspections, cleaning, lubrication, and proactive measures to ensure equipment reliability, safety, and longevity. Incorporating these key components into a comprehensive maintenance strategy can lead to cost savings, increased productivity, and a more sustainable operation.